High Conductivity Light Alloys for Next Generation Mobility:
The transportation industry will change more in the next ten years than in the last 100 years combined. Hybrid, battery electric and fuel cell powertrains contain battery trays, motor and inverter casings, conductor plates, battery cooling systems and in-car electronic casings to operate. These components as well as others must quickly absorb and dissipate heat (i.e. have high thermal conductivity) for efficient vehicle operation while still being lightweight, inexpensive and easy to manufacture. Conventional aluminum and magnesium alloys have the required strength/weight ratios for automotive applications. However, existing alloys were developed for combustion based automotive powertrains and do not have the requisite high thermal conductivity while still being easy to manufacture that next generation hybrid, electric and fuel cell powertrains demand. The below video and infographic demonstrate potential new alloys to meet these new requirements.
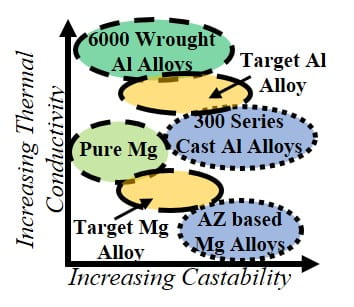
Magnesium Alloys for Biomedical Implant Applications:
The most commonly used technique for repairing large bone damage is bone grafting​. Magnesium has caught the attention of researchers due to its high biocompatibility with the human body and has been proposed as a suitable bone replacement material​. However, magnesium still has a high tendency to corrode and its mechanical properties are lower than that of bone and other metallic biomaterials​. Therefore, new magnesium alloys are needed for biomedical applications.
Aluminum Auxetic Structures Produced Using Combined Stereolithography and Investment Casting:
Investment casting produces structurally complex metal parts with good surface finish, and attractive mechanical properties. Metal additive manufacturing using either powder bed fusion or direct energy deposition technology allow wide design freedom; but is capital intensive. This study combines polymer additive manufacturing through the utilization of a stereolithography 3D printing and metal investment casting to produce complex geometry, lightweight structures for energy absorption in transportation applications. The below video demonstrates auxetic behaviour in a pure aluminum lattice.
Composite Food Packaging for Preservation:
Nearly a third of all fresh produce is wasted and not only is this unsustainable, it is a significant revenue loss to the entire food supply chain. Food packaging for fruits and vegetables is supposed to protect the food items, maintain quality and offer preservation by preventing moisture, mold and oxygen from reaching the food product. This proposal aims to develop a novel composite food packaging solution that will protect and maintain the food package atmosphere.